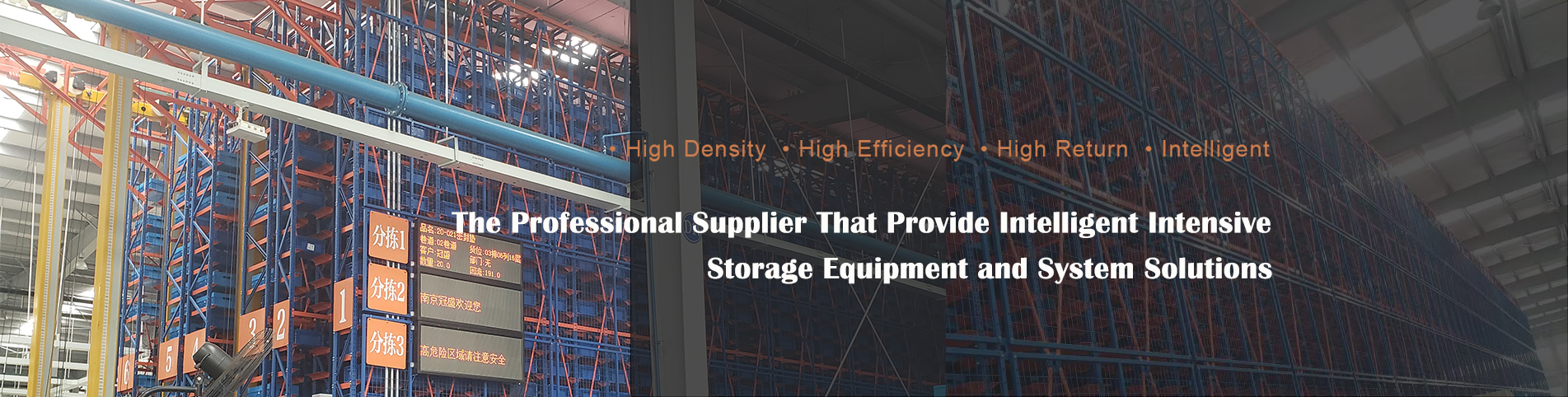
Four-way Shuttle system Features
EBILTECH Four-way Shuttle system Features:
Advantages and Characteristics:
1. The four-way shuttle is an intelligent handling device capable of both vertical and horizontal traveling.
2. The four-way shuttle is highly flexible, which can freely change the operation aisle. In addition, it is possible to adjust the system capacity by adding or reducing the number of shuttles. When necessary, a shuttle fleet may be established to respond to the system peak, thus solving the bottleneck of entry and exit operations.
3. Four-way shuttles are interchangeable. When a shuttle or lift fails, other shuttles or lifts can be dispatched by the dispatching system for completing the operation without affecting the system capacity.
4. The four-way shuttle is not only suitable for low-flow and high-density storage, but also suitable for high-flow and high-density storage. It can maximize the efficiency, cost and utilization of resources.
Heavy duty four-way shuttle performance:
Maximum travel speed: 2m/s
Maximum loading: 1.5T-2T
Light duty four-way shuttle performance:
Maximum travel speed: 4m/s
Maximum loading: 35kg-50kg
Energy unit: super capacitor
The pallet four-way shuttle is an intelligent device used for pallet cargo handling. It can achieve both vertical and horizontal travel, and can reach any position in the warehouse. The horizontal movement and retrieval of goods in the shelf is completed by only one four-way shuttle car. The level of system automation is greatly improved through hoisting. It is a new generation of intelligent handling equipment for pallet-type dense storage solutions.
Project Benefits:
High degree of intensiveness: 4 way shuttle racking system compared with the general warehouse, the inventory rate has increased by 20%~30%;
High degree of automation, four-way shuttle car + stacker+ WCS/WMS management system, realizes the NCC docking with the customer , and realizes fully automatic stock in and out;
The overall system has a high degree of flexibility, which is reflected in two aspects:
A. The left and right libraries are connected, and each set of four-way shuttle car and hoist is interchangeable. If a single system fails, the other three systems can be called at any time to achieve normal work in the warehouse;
B. The number of four-way shuttle car can be increased at any time according to the efficiency needs of customers.
Case show
Introduction of Design Scheme
Driven by DC motor, battery: 48V, 60AH;
Reversing and lifting of pallets adopt hydraulic method;
The control is completed by PLC.
Main control module
PLC (Siemens)
Advantages of Siemens PLC:
Famous brand, extremely high reliability;
Rich built-in integrated functions;
Rich expansion modules;
Strong communication capabilities.
Reasons for choosing PLC control:
Stability: When there is no need to process large amounts of data, PLC is more stable, especially for long-term applications;
Concise: PLC can directly control the driver and other components, and the industrial computer needs to add an unstable CAN module;
PLC has strong versatility and high penetration rate, and customers can operate the application through simple training.
Underlying logic algorithm
Pulse plus reading (remaining displacement):
Frid absolute addressing review, correction, address recognition.
Driving
Running and identification of the 4 way shuttle car
As shown in the figure, the driving process of the shuttle car from the original address (2, L) to the target address (7, AQ) will include driving and reversing actions. When the car travels from (2, L) to the first reversing point (7, L), a certain amount of pulse will be given.
Then in the process of driving, scan the address recognition chip on the cargo location continuously to update the pulse amount, and the RFID on the address recognition chip will verify whether the read address recognition chip is correct, and finally check the reversing position.
After the shuttle car arrives at (7, L), the reflective photoelectric on the trolley will fine-tune and correct the position, change direction after reaching the requirements, and then drive to (7, AQ) in the same way.
Reversing of the 4 way shuttle car
When the shuttle car reaches the reversing point, there will be two photoelectric devices to illuminate the correction film on the right. The correction length is 10.3CM, and the distance between the photoelectricity is 10CM. When one side of the photoelectric illuminates the correction film and the other side does not, the shuttle car will move to one side until both are illuminated, and then start the reversing procedure.
Machinery (accessories)
Standardized shuttle car body: 45# steel car body made of precise laser cutting, the cylinder body thickness reaches 22mm, and the loading capacity reaches more than 2 tons; laser cutting, high precision;
Using hydraulic jacking; heavy load; simple structure (solenoid valve control oil cylinder);
The design service life of the above components is 10 years;
Accurate measurement: laser technology is used to measure the length, width, height and diagonal of the car body, and the measurement accuracy is within 0.1mm.
Mechanical (track fit)
The wheel adopts a structure similar to that of a train wheel with a wheel edge and closely fits the track. The distance between the wheel edge and the track is only 1mm, which effectively solves the problem of driving deviation.
Hardware, software (the nerve center of the shuttle car)
Core of the shuttle : the shuttle use stable Siemens PLC as the main control module, plus specific logic algorithms to ensure error-free judgment and operation;
Electricity
Adopt the world's top brands Siemens, Schneider, NSK, strong stability and more reliable
Test
In order to check the quality and give a perfect shuttle car to the project site, the shuttle car must be tested in the field for 10 to 15 days. The test content mainly includes:
Fatigue test: Each 4 way shuttle car runs continuously in the test area for more than 8 hours a day.
Alternate operation of load and no-load: alternate operation of load and no-load, in line with general project scenarios.
Mechanical testing: testing of chain tension, gear bite, etc.
Electrical test: the stability of the trolley, heat generation and other tests.
Software testing: testing of car acceleration and deceleration, driving accuracy, signal acceptance status, etc.