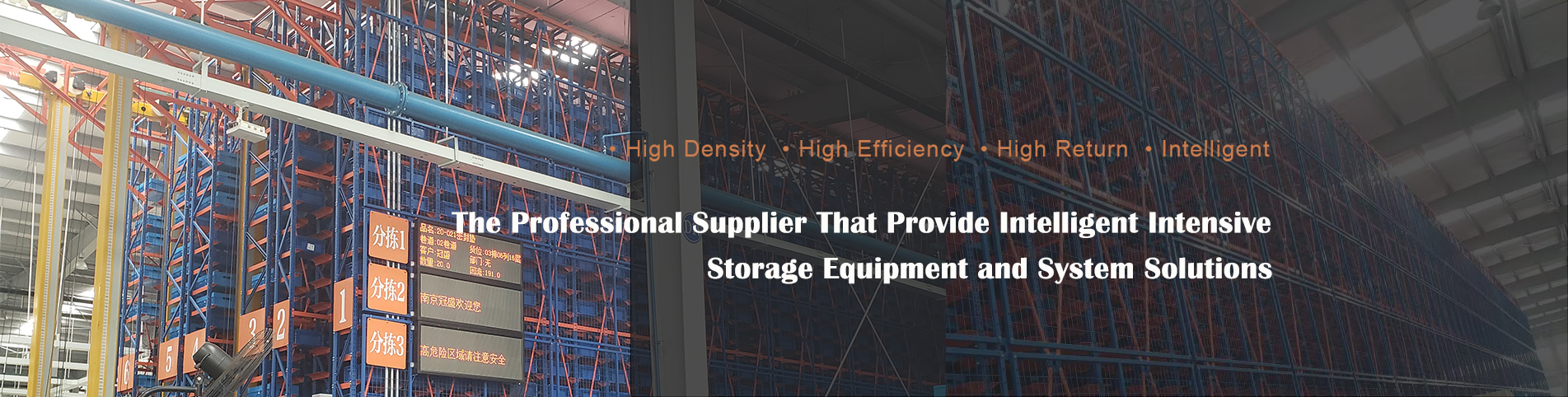
??10 Key Points to Consider in ASRS-Logistics Building Design
The design of an Automated Storage and Retrieval System (ASRS) logistics building plays a critical role in ensuring efficient operations and maximizing storage capacity. Here are 10 key points to consider:
Optimal Layout and Space Utilization:
Vertical Storage: Emphasize vertical storage solutions to make the most of available space. Utilize high-rise shelving and rack structures to maximize storage density.
Aisles and Pathways: Plan efficient aisles and pathways for automated machinery to navigate and access storage locations. Consider different aisle configurations based on the type of ASRS system.
ASRS System Selection and Integration:Crane-Based or Shuttle-Based ASRS: Decide between crane-based and shuttle-based ASRS systems based on factors like inventory volume, SKU diversity, and operational requirements. Ensure seamless integration with the overall warehouse layout.
Compatibility with WMS and Software: Ensure that the ASRS system integrates seamlessly with Warehouse Management Systems (WMS) and other software for optimal inventory management and control.
Safety and Compliance:
Safety Standards: Adhere to industry safety standards for ASRS systems, including proper guarding, safety interlocks, and emergency stop mechanisms to protect workers and equipment.
Compliance with Regulations: Ensure compliance with local and international regulations governing ASRS operations, including fire safety codes, seismic requirements, and building codes.
Material Handling Equipment:
Automated Conveyors and Robots: Select appropriate automated material handling equipment, such as conveyors, robotic arms, and shuttles, to facilitate efficient movement of goods within the ASRS system.
Integration with ASRS: Ensure seamless integration between material handling equipment and the ASRS system for smooth operations and minimal downtime.
Fire Suppression and Safety Systems:
Fire Suppression Technology: Implement advanced fire suppression systems like water mist, foam, or gas-based systems designed to protect goods and equipment in case of a fire emergency.
Smoke Detection and Alarm Systems: Install state-of-the-art smoke detection and alarm systems to provide early warning in case of smoke or fire events, allowing for timely evacuation and response.
Temperature and Environmental Controls:
Climate Control Systems: Consider the need for climate control, especially for storage of temperature-sensitive goods. Implement heating, ventilation, and air conditioning (HVAC) systems as required.
Humidity Management: Incorporate humidity control systems to prevent moisture-related damage to goods and equipment, particularly in environments with high humidity levels.
Power Supply and Backup Systems:
Redundant Power Supply: Implement redundant power supply systems, including generators and uninterruptible power supply (UPS) units, to ensure continuous operation of the ASRS system, even during power outages.
Emergency Power Off (EPO): Install Emergency Power Off switches at strategic locations to quickly shut down the ASRS system in case of emergencies or maintenance requirements.
Maintenance and Service Accessibility:
Service Platforms and Walkways: Design the ASRS structure with service platforms and walkways to provide safe access for maintenance personnel to perform routine inspections, repairs, and equipment servicing.
Spare Parts Storage: Allocate space for spare parts storage within the ASRS building to ensure quick access to critical components for timely maintenance and repairs.
Future Expansion and Scalability:
Modular Design: Plan for a modular and scalable design that allows for future expansion or reconfiguration of the ASRS system to accommodate changing business needs and increased inventory volumes.
Flexibility in Layout: Maintain flexibility in the layout to accommodate potential upgrades or additions to the ASRS system, including the integration of new technology and equipment.
Employee Training and Safety Protocols:
Training Programs: Develop comprehensive training programs for employees and operators responsible for ASRS operations. Ensure they are well-versed in safety protocols, emergency procedures, and equipment operation.
Safety Signage and Procedures: Clearly label and mark safety zones, emergency exits, and operational procedures within the ASRS building to promote a culture of safety among staff.
Designing an ASRS-logistics building requires meticulous planning and consideration of various factors to ensure the seamless operation of automated storage and retrieval systems. By prioritizing safety, efficiency, and scalability, businesses can create a high-performing logistics facility that meets the demands of modern warehousing operations.