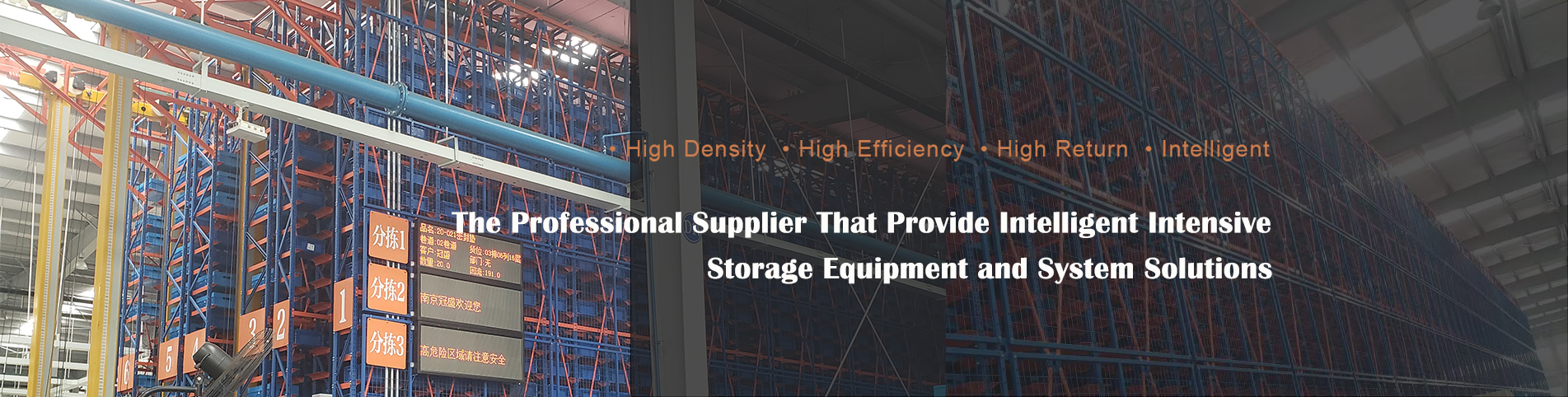
Pallet Shuttle Systems: What They Are and What They Do
If you want to maintain your facility¡¯s competitive edge, you need to leverage the latest warehouse technology to streamline inventory control processes, optimize space utilization, design and use technology that offers built-in redundancy, use technology that offers very high throughput availability in a reliable manner, use technology that will not cause loss of availability to stored inventory, and accelerate material handling processes.
While there are many ways to optimize your supply chain, pallet shuttle systems are one of the most effective technological solutions in warehousing. However, it¡¯s important to understand this potential solution before integrating it into your facility¡¯s operations as there are multiple flavors to choose from and choosing the right flavor is key to optimizing success.
Given proper design of a pallet shuttle system with N+1 redundancy of the lifts in combination with the pallet shuttles operating independently at a high level of redundancy, a properly designed pallet shuttle system creates a situation providing very high system throughput availability in a reliable manner and very high location and inventory accessibility with minimal potential for location blocking by failed shuttles or lifts, a much better situation than the typical crane based ASRS should a crane failure occur.
With that in mind, this guide to pallet shuttle systems will reveal to a large degree the factors you need to know about these robust technologies, including what they are, how they work, and some exciting trends that have recently emerged.
What Are Pallet Shuttle Systems?
Pallet shuttle systems are a form of warehouse automation technology that¡¯s rapidly changing how businesses manage storage and retrieval of its inventory. Pallet shuttle systems are another form of Automated Storage and Retrieval Systems (AS/RS).
They provide benefits like improved warehouse efficiency, reduced labor and high-density storage optimization. This is achieved utilizing controls and software that direct robotic shuttles to move throughout a rack system on a series of rails and lanes. As a result, pallet shuttle systems efficiently store and retrieve pallets with incredibly-fast efficiency.
Pallets are inducted via conveyor, AMRs or forklifts. Once inducted, the rack system utilizes shuttles to store and retrieve which means workers and forklifts don¡¯t navigate crowded aisles, reducing labor costs and further boosting operational efficiency.
Pallet Shuttle Systems vs. Cranes/Unit Loads and Forklifts
The best way to showcase what a pallet shuttle system is capable of is by comparing them to two other common pallet-moving tools: cranes and forklifts.
Forklifts: A pallet-moving tool that often has one of the highest FTE salaries in the warehouse and the cause of accidents and damage to product, rack, and infrastructure. A forklift also has limited height accessibility, unlike pallet shuttles.
AS/RS Cranes: A more expensive system that moves pallets up and down a single aisle to store and retrieve. This system has multiple points of failure which can negatively affect up time.
Many warehouses are familiar with these systems, but pallet shuttle systems are different for several reasons. Pallet shuttles have no single point of failure, easier maintenance, higher throughput, not reliant on workers showing up for their shifts, eliminating fork truck and human aisle congestion, and facility damage.
Additional key advantages that pallet shuttle systems offer are:
Flexibility to move more freely than an ASRS crane throughout the storage racking to shorten travel distances.
More parallel processing capability in the same space than an AS/RS crane. Pallet shuttles can simultaneously move on various levels in the same travel aisle due to multiple planes of travel and on different vertical storage levels.Pallet shuttles can utilize multiple shuttles in the same storage aisle on the same storage level. This is typically impossible for most ASRS cranes.
The scalability of pallet shuttles is superior to ASRS cranes. This is due to their plug-n-play capability. Additional shuttles can be dropped into an existing system to increase throughput capability without any racking changes required. Except for adding some additional charging locations for the shuttles to refuel.
Final notes of value add proposition:
For those operating refrigerated and/or frozen warehouses, the pallet shuttles offer the reduction of reliance on people to operate forklifts in a frozen environment.
Build your pallet storage over your fulfillment operations to use all your vertical space!
How Pallet Shuttle Systems Work
To appreciate the role pallet shuttle systems play in creating a lean warehouse, here¡¯s a closer look into how they operate.
1. Modular Design
Because the system is modular, the pallet shuttles move independently and constantly throughout the system completing put-away tasks and interleaving move tasks for reorganization and picking tasks for order fulfillment. This independent operation of the shuttles means that multiple applications can also be conducted with proper software guidance to simultaneously support such operations as: goods-to-person case picking, robotic case picking, robotic layer picking, full pallet delivery to staging lanes for shipping, short term pallet buffering, longer term pallet storage in both selective storage and deep lane configurations in the same system, inventory cycle and quality control inspections, among other potential functionals all at the same time.
With 2D pallet shuttles, the shuttles can migrate to where the work is within the 2D storage plane. With 3D pallet shuttles, the shuttles can migrate to any place on any level to get to where the work currently is, allowing for pallet shuttle resources to maximize their utilization. To add even more value to the future possibilities of your warehouse, pallet shuttle systems, due to their modularity, can increase the storage racking and/or increase the throughput easily without need to take down any part of the system, i.e. while maintaining your service levels without interference.
2. Increased Up Time ¨C No Single Point of Failure
One of the standout features of pallet shuttle systems is it incorporates no single point of failure for the shuttles. Now, the lifts can create a point of failure, but by properly designing the lifts to have multiple lifts in the design, you can essentially create a zero point of failure system. This means that each component of the system functions as an individual component and has designed redundancy to keep the system running at all times.
If an element of the system malfunctions, your entire operation doesn¡¯t stop, only a small percentage of impact will occur to keep you virtually 100 percent. The system continues to perform and the maintenance staff can simply replace the damaged component during a down shift or more convenient time. Also, pallet shuttles can usually be removed from the system for maintenance and/or repair within minutes and without impacting the operations of other lifts and pallet shuttles.
This simple design translates to easier maintenance, reduced overall costs, and less overall downtime. Keeping downtime to a minimum is critical for maximizing throughput capacity and meeting your productivity goals.
3. Robotics Technology & Software Drives Value
Robotics technology plays a pivotal role in the automated function of pallet shuttle systems. Each pallet shuttle is usually equipped with its own on-board computer and communications networking switches for wireless communication and operation. The pallet shuttle system utilizes robotic shuttles and lifts to store and retrieve pallets in your warehouse.
Conversely, the lifts are simple up-down movement devices and therefore highly reliable and require minimal intelligence and software direction. The pallet shuttles run within the storage racking system on what could be on a single level or on multiple levels high, depending on your facility¡¯s specific requirements such as: facility parameters (footprint, clear height, etc.), storage capacity (pallets to store by height of pallet), throughput (pallets in and pallets out as it varies throughout the daily operation), budget, service levels, and parallel processes to support.
WIth that said, it is important to have a strong and robust software system such as a Warehouse Execution Systems (WES) software driving the multiple parallel processes to balance pallet shuttle and lift resources over the various move tasks while properly prioritizing those tasks on the fly to make sure all service levels are met and that processes are properly served to optimize your operational objectives.
This WES or driving software operates the pallet shuttle by creating and prioritizing tasks to release them at the correct time to the optimal robotic pallet shuttle. Then the robotic pallet shuttle uses its onboard processor and its shuttle routing software to optimize and control movement to perform the given tasks.
3. The Environmental Value Play
The robotic pallet shuttle is the heart of the pallet shuttle system. The shuttle moves beneath pallets, carefully lifts them, and transports them to a predefined destination. The shuttle is also battery-powered, making it a valuable part of a sustainable warehousing operation. You can use the battery-powered shuttle system to decrease your reliance on fossil fuels, shrink your carbon footprint, and position your brand as an environmentally friendly organization.
Applications and Use Cases
Pallet shuttle systems are incredibly versatile when it comes to the industries and applications they serve..
Pallet Shuttle application examples:
Goods-To-Person Or Robot Storage & Retrieval: Feed manual case picking stations, goods-to-robot case picking cells, goods-to-robot layer picking cells, or just pick full pallets out in sequence.
Work-In-Process Buffer: Store pallets short term or long term between process areas/zones to decouple and provide great responsiveness to downstream processes. Delivering pallets out of storage in various levels of sequence tightness based on what is required, e.g. exact sequencing (hardest) or 1 within Y sequencing (as Y increases the flow or sequencing gets easier). Exact or near exact sequencing can be used to load trailers in reverse delivery sequence. For example, feeding sequenced pallets to a picking cell to build stable outbound pallet(s) from the source pallets to enable building of a pre-calculated optimized outbound pallet.When used as a buffer, the pallet shuttle system really allows one area to work ahead of another and enables such benefits as smoothing of workload in upstream processes and maximizing resource utilization. Then downstream operations can request pallets and have them delivered at the desired pace, e.g. to quickly load an outbound trailer when it shows up.
Reserve Storage & Retrieval: Store pallets in deep storage for reserve storage applications and configure and change how lanes of storage are configured to match inventory mix of pallets on hand. Also, a huge point related to this application is to build the reserve storage pallet shuttle system over the order fulfillment operation to maximize the cube utilization of your facility.The modular pallet shuttle system also allows you to only buy the number of pallet shuttles necessary to meet throughput rate instead of buying ASRS cranes that are locked into certain aisles and with limited mobility versus the shuttles.
To name just a few!
Moving on to use cases, Pallet Shuttles can support the needs of a wide range of industries, including but not limited to:
E-Commerce: With rapid loading and unloading capabilities, pallet shuttles help e-commerce giants maintain fast delivery operations
Manufacturing: Pallet systems offer compact storage solutions, allowing manufacturers to maximize storage space.
Food and Beverage: The efficiency of pallet shuttles ensure products with the nearest expiration dates are shipped out first, reducing inventory waste.
Pharmaceuticals: Pallet shuttles offer the precision pharmaceutical companies need to ensure the right medications reach the right destination.
Automotive: Pallet shuttles optimize storage and simplify parts retrieval in the automotive industry, which relies on organized, accessible storage solutions.
Textiles: Rolls of fabric that vary in size, shape, and weight can be challenging to store and retrieve, but pallet shuttles offer adaptability, adjusting to different load sizes to retain the textiles¡¯ condition.
Retail: As a retail business grows, so does its inventory; whether it¡¯s a supermarket chain or an apparel retailer, pallet shuttles can handle diverse products and make inventory management easier.
Ambient, Chilled or Frozen Environments: The pallet shuttle system can operate in environments ranging from 113 degrees fahrenheit to minus 33 degrees fahrenheit.
Pallet shuttle systems cater to an array of industries thanks to their unmatched flexibility. The high density footprint of pallet shuttles allows warehouses to implement them reclaiming otherwise wasted and valuable floor space.
If you¡¯re interested in implementing this warehousing solution, there are three primary factors you should consider first.
3 Factors to Consider Before Implementing a Pallet Shuttle System
1. Budget
Pallet shuttle systems can be a great investment for your facility. However, there¡¯s a CAPEX cost associated with installing a pallet shuttle. That being said, make sure you carefully consider all expenses, including the cost of the unit itself and the associated installation and training expenses. Then calculate the savings that a pallet shuttle provides including less floor space, labor, forklifts, damage, and higher throughput and accuracy. By comparing and calculating the return on investment (ROI) most organizations find a pallet shuttle to be a wise investment.
2. Layout
The physical layout of your warehouse is key to successful impleme
Is a Pallet Shuttle System Right for You?
As storage requirements continue to increase, warehouse space continues to increase in cost, and robotics and automation technologies continue to advance, pallet shuttle systems will become even more indispensable to warehousing operations.
Pallet shuttle systems represent the future of warehousing, blending human expertise with cutting-edge technology and software. Their promise of scalability, adaptability, and efficiency position them as true game-changers for your organization. The question isn¡¯t if you should consider pallet shuttle systems, but when.