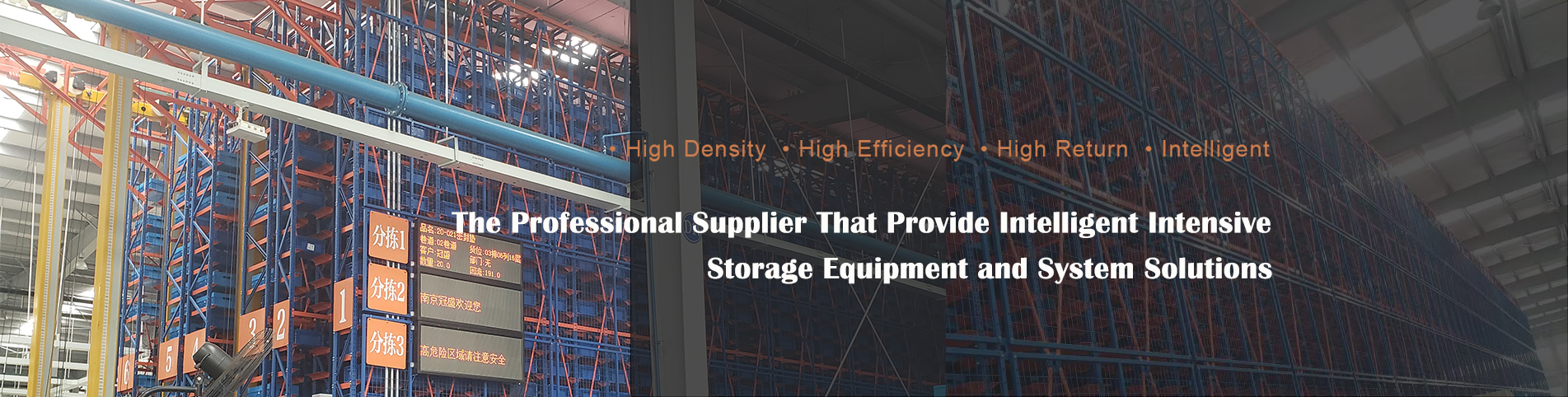
Radio Shuttle and Stacker Crane Case
This project is divided into three cold warehouses and one normal temperature warehouse:
Normal temperature warehouse: The general design of the system is 9138 pallets positions. Through 1 stacker, 5 shuttle cars and conveying equipment to realize
the function of automatic inbound and outbound.
The pallet labels are all barcoded for information management, and external dimension detection and weighing are provided before storage to ensure the safe
storage of goods.
The automated high-density Radio Shuttle + Stacker Crane Racking System utilizes the characteristics of stacker crane that running in the front/back and up/down
directions of the main aisle, and radio shuttle running in guild rail. The two devices are dispatched and coordinated through WCS software to complete the picking
and placing of goods.
Main working principle:
1. Inbound: After automatic stacking, the products are sent to the storage place of the three-dimensional warehouse through the conveying line. The stacker takes
the pallets and places them at the end of the tunnel allocated by WMS software. The goods are transported another end by the shuttle. The same batch products
are stored in the same lane.
2. Outbound: The shuttle will move the designated goods to the end of the tunnel and the stacker will pick up the goods through the forks, place them on the
outbound conveyor line, and then the goods can be picked up and shipped by forklifts or other handling equipment.
Radio Shuttle + Stacker High Density Automated Storage Racking System
¢Ù Fully automated processes to improve work efficiency and greatly reduce working time;
¢ÚGood safety, reducing forklift collision;
¢ÛHigh-density storage, the utilization rate of the warehouse is much higher than that of the roadway stacker racking system;
¢ÜHigh cost performance, the cost is lower than that of roadway stacker racking system;
¢ÝFlexible operation method
With the core of high efficiency, informationization, traceability and automation, this project meets the future market demand of fast inspection and quarantine,
fast entry and exit, bonded storage, fast sorting and traceability of imported fresh, meat, and aquatic products. Apply RFID technology to perceive positioning,
process traceability, information collection, item sorting and picking, etc., write product quarantine inspection, transportation, storage, handover and other
information into the coding system, and realize product production, transportation, and storage by scanning bar codes or identifying RFID information The t
wo-way traceability of information such as, handover, etc. realizes the identification of anti-counterfeiting and safety functions, ensuring food safety and drug
safety, and ensuring the authenticity of products. The application of intelligent shuttle technology in the field of automated warehouses, through the combination
of intelligent shuttle systems and dense shelves, greatly improves the space utilization rate of storage facilities and saves land.